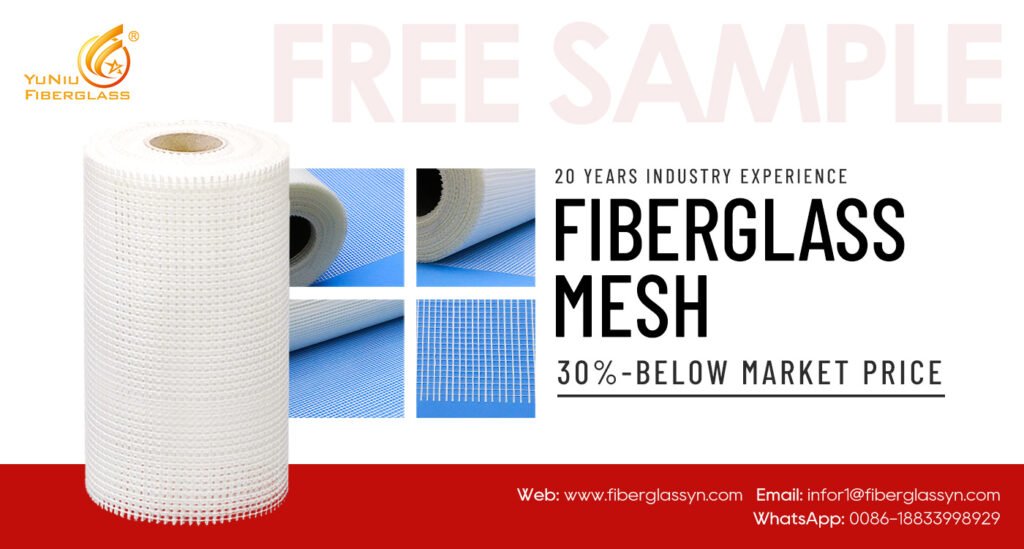
Introduce
Fiberglass Mesh, as a high-performance composite reinforcement material, plays an increasingly important role in modern construction and industry. Its light weight, high strength, corrosion resistance and other characteristics make it widely used in many fields. This article will focus on the cutting performance, waterproofness, fire resistance and melting point of fiberglass mesh, and evaluate its value to help readers fully understand the characteristics and applications of this material.
Can you cut fiberglass mesh?
The cutting performance of fiber glass mesh is an important indicator for evaluating its processing and ease of use. Whether the fiberglass mesh can be cut easily and accurately directly affects its effect and efficiency in practical applications.
Cutting tools
- Hand tools: Commonly used cutting tools include scissors, utility knives, etc. These tools are simple to operate and suitable for small-scale or fine cutting work.
- Electric tools: For large-scale or complex cutting tasks, electric cutting machines such as electric shears and electric saws can be used. Electric tools have fast cutting speed and high precision, and are suitable for industrial production.
Cutting Tips
- Keep tools sharp: Whether it is a hand tool or a power tool, it is very important to keep the knife sharp. A dull knife will cause uneven cutting and even damage the fiber.
- Avoid pulling: During the cutting process, try to avoid pulling the fiberglass mesh to avoid fiber breakage or uneven edges.
- Use a support: When cutting a large area of fiberglass mesh net, you can place a flat support underneath, such as a wooden board or a cutting mat, to ensure a flat cutting surface.
Cutting effect
- Edge neatness: High-quality fiberglass mesh has neat edges and less fiber damage after cutting. If the cutting tool is not selected properly or the operation is improper, it may cause rough edges, affecting the appearance and use effect.
- Fiber damage: The damage to the fiber should be minimized during the cutting process to maintain the strength and performance of the fiberglass mesh. Using sharp knives and correct cutting techniques can effectively reduce fiber damage.
Practical application
- Building exterior wall: In the repair of cracks on the building exterior wall, the fiberglass mesh needs to be precisely cut to fit cracks of different shapes. This task can be easily accomplished using scissors or a utility knife.
- Roof waterproofing: In roof waterproofing projects, the fiberglass mesh needs to be cut to fit roof structures of different shapes. Using an electric cutting machine can improve work efficiency and ensure cutting effect.
Is fiberglass mesh waterproof?
The waterproof performance of fiberglass mesh is an important indicator for evaluating its application in humid environments. The waterproof performance of fiberglass mesh is affected by many factors, including material properties, coating materials and use environment.
Material properties
- Glass fiber: Glass fiber itself has good water resistance and chemical stability, is not easy to absorb water and swell, and is suitable for use in humid environments.
- Coating material: The coating material on the surface of the fiberglass mesh has a significant effect on its waterproof performance. Commonly used coating materials include latex, epoxy resin, polyurethane, etc. These coating materials can not only improve the waterproof performance of the fiberglass mesh, but also enhance its chemical resistance and weather resistance.
Coating effect
- Improve waterproofness: The coating material can fill the tiny pores in the fiberglass mesh to form a dense waterproof film, which effectively prevents water penetration.
- Enhance adhesion: The coating material can also improve the adhesion between the fiberglass mesh and the substrate, ensuring the stability and durability of the waterproof layer.
Test method
- Immersion test: Soak the fiberglass mesh sample in water for a certain period of time, observe its water absorption and size changes, and evaluate its waterproof performance.
- Water spray test: Fix the fiberglass mesh sample on the test bench, use a water spray device to simulate rain impact, and observe its waterproof effect.
- Wet and hot cycle test: Repeatedly cycle the fiberglass mesh sample in a wet and hot environment to evaluate its stability and durability in a long-term humid environment.
Practical application
- Roof waterproofing: In roof waterproofing projects, the use of fiberglass mesh with waterproof coating can significantly improve the waterproof performance of the waterproof layer, prevent rainwater penetration, and protect the internal structure of the building.
- Basement waterproofing: In basement waterproofing projects, the use of fiberglass mesh with waterproof coating can effectively prevent groundwater penetration and improve the waterproof effect of the basement.
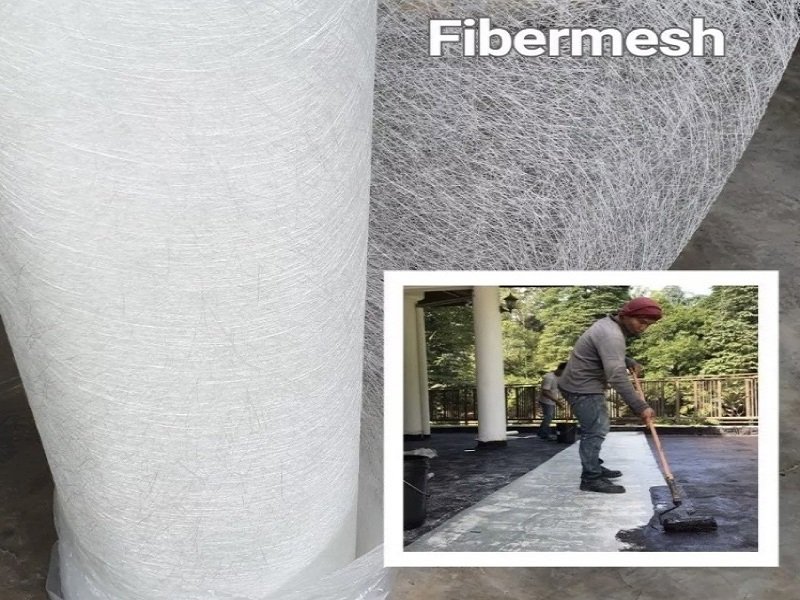
Is fiberglass mesh flammable?
The fire resistance of fiberglass mesh is an important indicator for evaluating its application in fire-hazardous environments. The fire resistance of fiberglass mesh is affected by many factors, including material properties, coating materials, and use environment.
Material properties
Glass fiber: Glass fiber itself has good fire resistance, is not easy to burn, and is suitable for fire-hazardous environments.
Coating material: The coating material on the surface of the fiberglass mesh has a significant effect on its fire resistance. Commonly used coating materials include flame-retardant latex, epoxy resin, polyurethane, etc. These coating materials can improve the fire resistance of fiberglass mesh, making it less likely to burn in a fire.
Fire protection grade
- Grade A: The highest fire protection grade, suitable for places with extremely high requirements for fire protection performance, such as high-rise buildings, public places, etc.
- Grade B1: The second highest fire protection grade, suitable for places with certain requirements for fire protection performance, such as ordinary buildings, home decoration, etc.
Test method
- Vertical combustion test: Fix the fiberglass mesh sample vertically on the test bench, ignite it with a flame, observe its burning time and self-extinguishing time, and evaluate its fire resistance.
- Horizontal combustion test: Fix the fiberglass mesh sample horizontally on the test bench, ignite it with a flame, observe its burning speed and flame spread, and evaluate its fire resistance.
- Smoke density test: Burn the fiberglass mesh sample in the test furnace, measure the smoke density it produces, and evaluate its smoke release in a fire.
Practical application
- Building exterior wall: In the fire isolation layer of the building exterior wall, the use of fiberglass mesh with fireproof coating can significantly improve the fire resistance of the exterior wall and prevent the spread of fire.
- Fireproof isolation layer: In industrial plants and warehouses,fiberglass mesh with fireproof coating can effectively isolate the fire source and prevent the spread of fire.
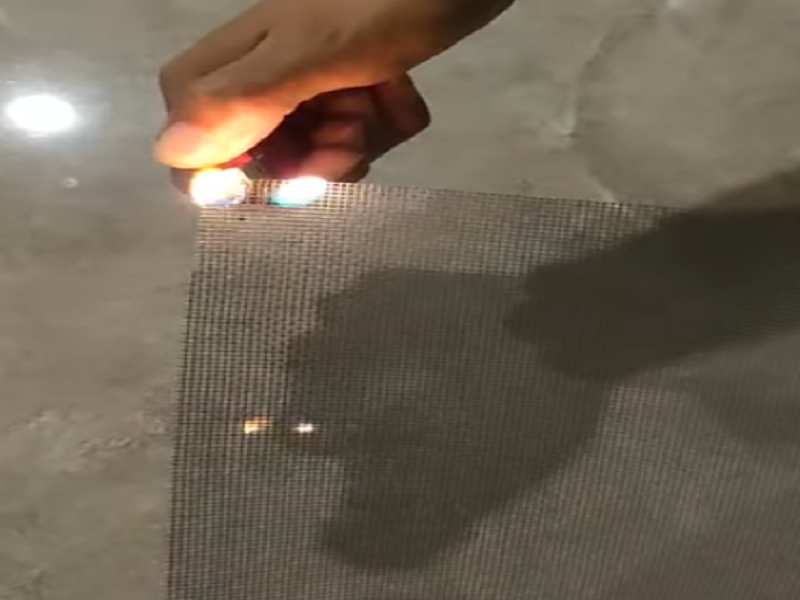
Does fiberglass mesh melt?
The melting point of fiberglass mesh is an important indicator for evaluating its application in high temperature environment. The melting point of fiberglass mesh is affected by many factors, including material properties, coating materials and use environment.
Material properties
- Glass fiber: The melting point of glass fiber mesh is relatively high, usually above 1000°C. In high temperature environment, glass fiber mesh can maintain stable performance and is suitable for high temperature working environment.
- Coating material: The coating material on the surface of fiberglass mesh has a significant effect on its melting point. Commonly used coating materials include high temperature resistant latex, epoxy resin, polyurethane, etc. These coating materials can improve the temperature resistance of fiberglass mesh, making it difficult to melt in high temperature environment.
Temperature resistance
- Maximum use temperature: The maximum use temperature of fiberglass mesh refers to the maximum temperature it can withstand in long-term use. The maximum use temperature of common fiber mesh can reach 300°C, which is suitable for high temperature working environment.
- Short-term temperature resistance: The short-term temperature resistance of fiberglass mesh refers to the maximum temperature it can withstand in a short period of time. Common fiberglass mesh has a short-term temperature resistance of up to 500°C, which is suitable for environments with short-term high temperature shock.
Test method
- Thermogravimetric analysis: The mass loss of fiberglass mesh at different temperatures is measured by a thermogravimetric analyzer to evaluate its temperature resistance.
- Differential scanning calorimetry: The heat flow change of fiberglass mesh at different temperatures is measured by a differential scanning calorimeter to evaluate its melting point and phase change temperature.
- High temperature test: The fiberglass mesh sample is heated in a high-temperature furnace, and its morphological changes at different temperatures are observed to evaluate its temperature resistance.
Practical application
- High-temperature pipeline: In high-temperature pipelines, the use of fiberglass mesh with high-temperature resistant coating can significantly improve the temperature resistance of the pipeline and prevent the erosion of the pipeline by high-temperature media.
- Industrial furnace lining: In industrial furnace lining, the use of fiberglass mesh with high-temperature resistant coating can effectively protect the furnace lining and extend the service life of the furnace lining.
Is fiber mesh worth it?
As a high-performance composite reinforcement material, the value of fiberglass mesh is not only reflected in its excellent performance, but also in its wide application and cost-effectiveness.
Performance advantages
- Cutting performance: The fiberglass mesh is easy to cut and can be easily adapted to the application requirements of various shapes and sizes.
- Waterproof performance: The fiberglass mesh has good waterproof performance and is suitable for applications in humid environments.
- Fireproof performance: The fiberglass mesh has good fireproof performance and is suitable for applications in fire-hazardous environments.
- Heat resistance: The fiberglass mesh has high temperature resistance and is suitable for applications in high temperature environments.
Wide application
- Interior wall insulation: In the interior wall insulation system, the use of eifs fiberglass mesh can significantly improve the crack resistance and durability of the insulation layer, and prevent cracking caused by temperature changes. The fiberglass mesh can also enhance the adhesion of the insulation material, ensure the close combination between the insulation layer and the wall, and improve the overall insulation effect.User feedback shows that the exterior wall finishing system using fiberglass mesh has better crack resistance and wind pressure resistance, significantly improving the service life of the exterior wall.
- External wall reinforcement: In the external wall finishing system, eifs fiberglass mesh can significantly improve the strength and durability of the external wall paint, plaster layer and tile bonding layer, and prevent the external wall from cracking and falling off.fiberglass mesh can also improve the waterproof performance of the external wall, prevent rainwater from penetrating, and protect the internal structure of the building from damage.User feedback shows that the exterior wall finishing system using fiberglass mesh has better crack resistance and wind pressure resistance, significantly improving the service life of the exterior wall.
- Roof waterproofing: The use of fiberglass mesh for roof waterproofing can significantly improve the crack resistance and penetration resistance of the waterproof layer, ensuring that the roof maintains a good waterproof effect for a long time.fiberglass mesh can also improve the adhesion of waterproof materials, ensure the close combination between the waterproof layer and the base layer, and prevent moisture penetration.User feedback shows that the roof waterproofing layer using fiberglass mesh has better waterproof performance and weather resistance, significantly improving the waterproof effect of the roof.
- Marble backing: In the processing and installation of marble, the use of fiberglass mesh can significantly improve the crack resistance and flexural strength of marble slabs, and prevent damage during transportation and installation. Fiberglass mesh can also improve the adhesion between marble and adhesives, ensuring that the marble slabs are firmly attached to the wall or ground.User feedback shows that marble slabs using fiberglass mesh have better crack resistance and flexural strength, significantly improving the installation quality and aesthetics of marble.
- Cement board and gypsum board: In the manufacture and installation of cement board and gypsum board, fiberglass mesh for cement board and gypsum board can significantly improve the crack resistance and flexural strength of the board, and prevent damage during transportation and installation.fiberglass mesh can also improve the waterproof performance of the board, prevent moisture penetration, and extend the service life of the board. User feedback shows that cement board and gypsum board with fiberglass mesh have better crack resistance and bending strength, which significantly improves the service life of the board.
- Mosaic: In the manufacture and installation of mosaics, fiberglass mesh for Mosaic can significantly improve the crack resistance and flexural strength of mosaics, and prevent damage during transportation and installation.fiberglass mesh can also improve the adhesion between mosaics and adhesives, ensuring that mosaics are firmly attached to the wall or ground. User feedback shows that mosaic with fiberglass mesh has better crack resistance and flexural strength, which significantly improves the installation quality and aesthetics of mosaic.
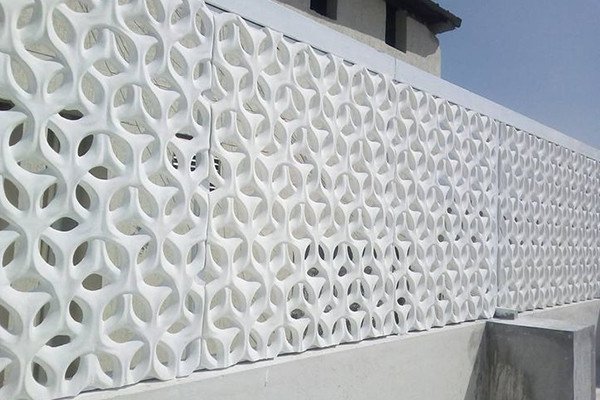
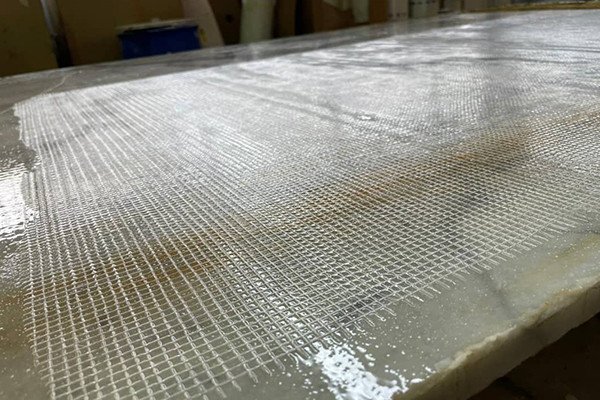
In Conclusion
As a high-performance composite reinforcement material,fiberglass mesh has significant advantages and broad application prospects in terms of cutting, waterproofing, fire resistance and temperature resistance. The fiberglass mesh has excellent cutting performance and is easy to adapt to application requirements of various shapes and sizes; good waterproof performance, suitable for applications in humid environments; excellent fire resistance, suitable for applications in fire-hazardous environments; high temperature resistance, suitable for applications in high temperature environments. In addition,fiberglass mesh has higher cost-effectiveness and a wider range of applications compared to other materials, and is worthy of promotion and use in various applications.
I hope this article can help readers fully understand the characteristics and applications of fiberglass mesh. If you have any questions or needs, please feel free to contact us. We will wholeheartedly provide you with professional technical support and services to jointly promote the application and development of fiberglass mesh in various fields.