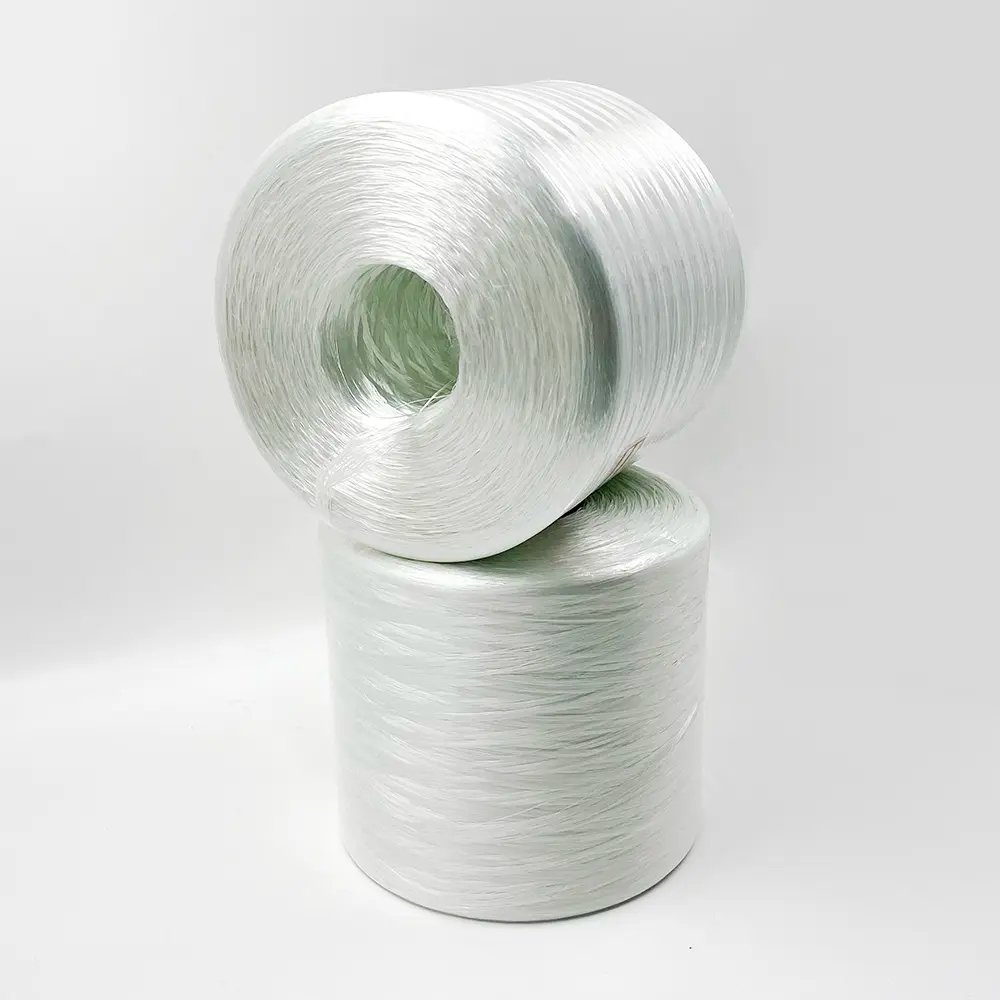
Introduction
With the accelerated development of industrialization, the research and development of new materials has become one of the important forces to promote scientific and technological progress. As a high-performance inorganic non-metallic material, glass fiber alkali-resistant yarn has received widespread attention and application in recent years. It not only has excellent mechanical properties, such as high strength and high modulus, but also has good chemical stability, especially its resistance to alkaline environments. These unique properties make glass fiber alkali-resistant yarn one of the indispensable materials in many industrial fields. With its excellent performance and broad application prospects, glass fiber alkali-resistant yarn plays an increasingly important role in modern industry.
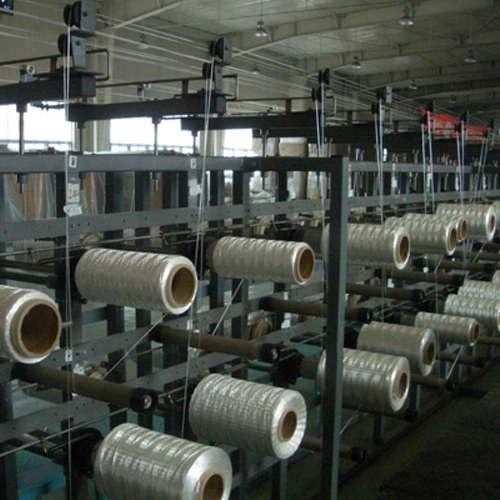
Overview of glass fiber alkali-resistant yarn
Definition
Fiberglass alkali-resistant yarn is a special glass fiber product that mainly achieves good resistance to alkaline environments by adjusting the composition ratio of glass raw materials. Although traditional glass fibers have high strength and good insulation properties, they are easily corroded in alkaline environments, resulting in reduced strength and shortened service life. In order to solve this problem, researchers have developed glass formulas containing higher levels of aluminum oxide (Al₂O₃), magnesium oxide (MgO) or other alkali-resistant components, so that the prepared glass fibers can maintain stable physical and chemical properties even in high-alkalinity environments. Alkali-resistant yarns are usually in the form of filaments or yarns, and can be woven, weaved or blended according to the needs of different application scenarios.
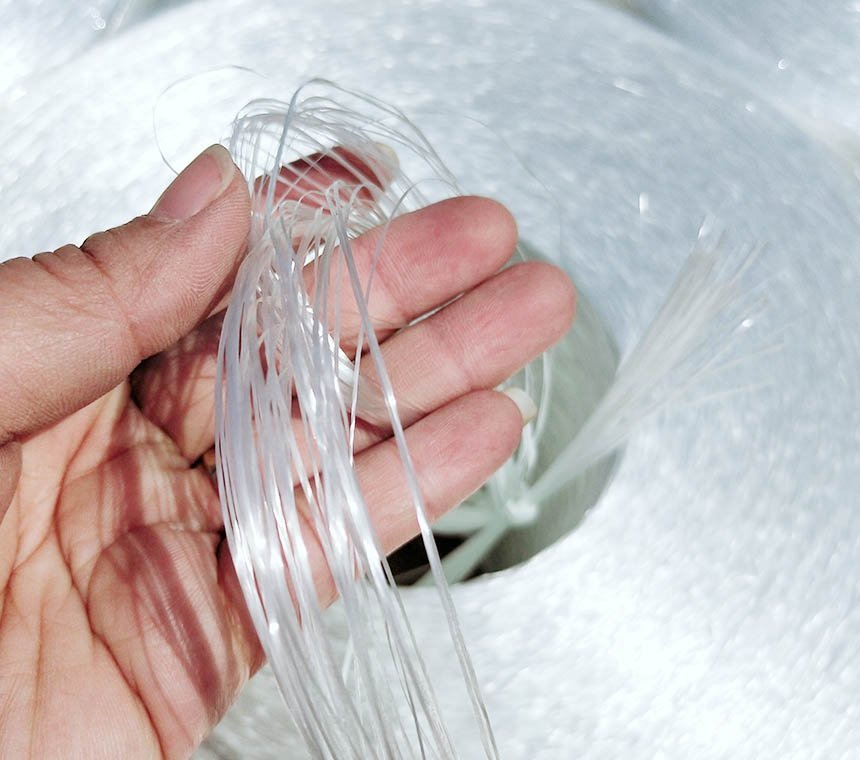
Development History
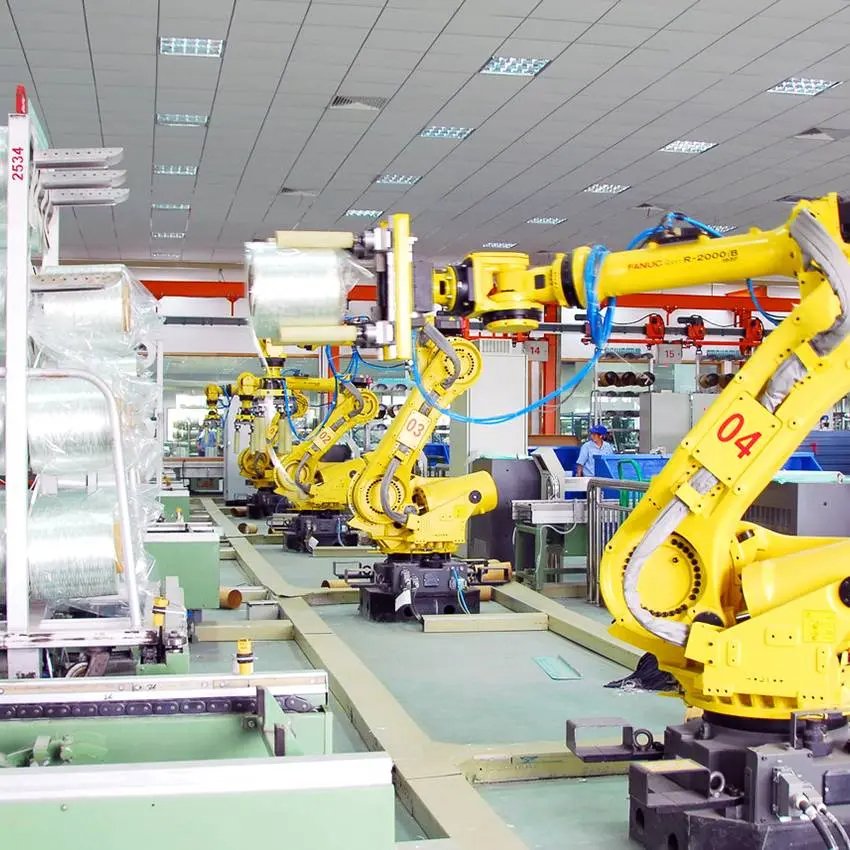
The history of glass fiber alkali-resistant yarn can be traced back to the end of the last century, when the construction industry’s requirements for material durability continued to increase, and the limitations of traditional glass fiber in alkaline environments gradually emerged. Especially for glass fiber used in concrete structures, because concrete itself has a certain alkalinity (pH value is about 12), ordinary glass fiber begins to degrade after a few years, which in turn affects the safety and service life of the entire building structure.
In order to overcome this problem, researchers began to explore new glass formulas. After years of experimental research, they successfully developed glass fiber with good alkali resistance. The initial application was mainly concentrated in the construction field, used to enhance the stability of concrete structures and extend their service life. With the passage of time and technological advancement, the application scope of glass fiber alkali-resistant yarn has gradually expanded to more fields, such as composite materials, the electronics industry, and the environmental protection industry.
Features
- Alkali resistance: This is one of the most prominent features of glass fiber alkali-resistant yarn. Even in a high alkalinity environment, the alkali-resistant yarn will not age or degrade significantly, thus ensuring the long-term stability and reliability of the material.
- High strength: Compared with ordinary glass fiber, alkali-resistant yarn also has higher tensile strength and bending strength, which enables it to maintain a good shape under greater stress.
- Lightweight: Glass fiber alkali-resistant yarn has a low density, light weight, and is easy to construct and install. It is particularly suitable for construction projects that need to reduce self-weight.
- Corrosion resistance: In addition to alkali resistance, alkali-resistant yarn also has good resistance to corrosive substances such as acid and salt spray, and is suitable for applications under various harsh environmental conditions.
- Electrical insulation: Good electrical insulation properties make glass fiber alkali-resistant yarn have a wide range of application prospects in electrical equipment, cable sheaths, etc.
- Easy to process: Glass fiber alkali-resistant yarn can be woven, cut or mixed according to different needs, with strong adaptability, which is convenient for users to flexibly choose the use method according to actual conditions.
Manufacturing process of alkali-resistant glass fiberroving
Raw materials
The production of glass fiber alkali-resistant roving depends first on the selection of appropriate raw materials and precise proportions. The main raw materials include quartz sand, soda ash, limestone, boric acid and other additives such as alumina (Al₂O₃), magnesium oxide (MgO), etc. Among them, Al₂O₃ and MgO are added to improve the alkali resistance of the final product. The reasonable combination of these ingredients can ensure that the glass fiber can still maintain good mechanical properties and chemical stability in an alkaline environment.
In order to obtain the best performance of glass fiber alkali-resistant yarn, the selection of raw materials must be strictly controlled. For example, quartz sand needs to be pure and free of impurities to ensure that the molten glass has a uniform chemical composition; soda ash and limestone are used to adjust the viscosity of the glass and reduce the melting point; and boric acid helps to improve the fluidity of the glass, making the subsequent fiber drawing process smoother.
Before officially putting into production, all raw materials need to go through pretreatment steps, including cleaning, drying, crushing and other processes to remove impurities and achieve a suitable particle size distribution. The work at this stage is directly related to the quality of subsequent smelting, so it must be strictly implemented.
Production process
- Melting is the first step in the production of alkali-resistant glass fiber yarn. The pre-treated raw materials are mixed in a certain proportion and sent to the furnace, where they are heated to a completely molten state under high temperature conditions (generally 1400℃~1600℃). The internal design of the furnace needs to take into account the effective distribution of heat to ensure that the temperature of the glass liquid is uniform and stable.
- The molten glass liquid is then introduced into the drawing tower and formed into long and thin fibers through the nozzle (leakage plate). In this process, the control of temperature and pressure is crucial, which directly affects the consistency of fiber diameter and surface finish. In addition, the cooling wind speed also needs to be precisely adjusted to avoid deformation or breakage of the fiber before solidification.
- After drawing, the glass fiber needs to undergo a series of post-processing processes to become the final product. It mainly includes coating, bundling and winding. The coating layer not only enhances the bonding strength between fibers, but also provides additional protection; bundling is to combine multiple monofilaments into one or more bundles of yarn; finally, the yarn is rolled into a form that is convenient for storage and transportation through a winding machine.
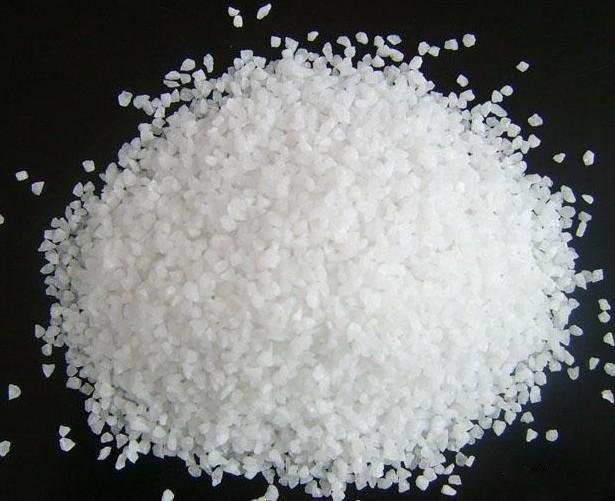
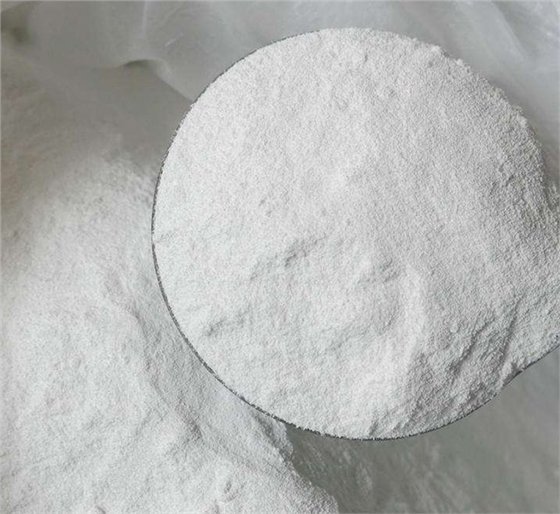
Analysis of the application of glass fiber alkali-resistant yarn in the industrial field
- Concrete reinforcement
One of the most important applications of glass fiber alkali-resistant yarn in the construction industry is as a concrete reinforcement material. Traditionally, steel bars are widely used to increase the strength and stability of concrete structures, but steel bars are easily corroded by chloride ions in alkaline concrete environments, causing rust, which in turn affects the durability and safety of buildings. In contrast, glass fiber alkali-resistant yarn not only has excellent mechanical properties, but also shows excellent stability in alkaline environments and will not fail due to corrosion. Therefore, it is increasingly used as a reinforcement material to replace steel bars, especially in infrastructure construction such as bridges, tunnels, and roads. - External wall insulation
Under the development trend of energy-saving buildings, external wall insulation systems (External Thermal Insulation Composite Systems, ETICS) have become increasingly important. Glass fiber alkali-resistant yarn is often used to make mesh cloth for the bottom reinforcement of external wall insulation systems to improve the overall strength and durability of the system. In addition, it can prevent cracking and improve the flatness and aesthetics of the finishing layer. - Interior decoration
In interior decoration, glass fiber alkali-resistant yarn is also used to make various decorative materials, such as wallpaper, ceiling panels, etc. These materials not only have good decorative effects, but also have functions such as fire prevention and sound insulation, which improve the comfort and safety of the living environment.
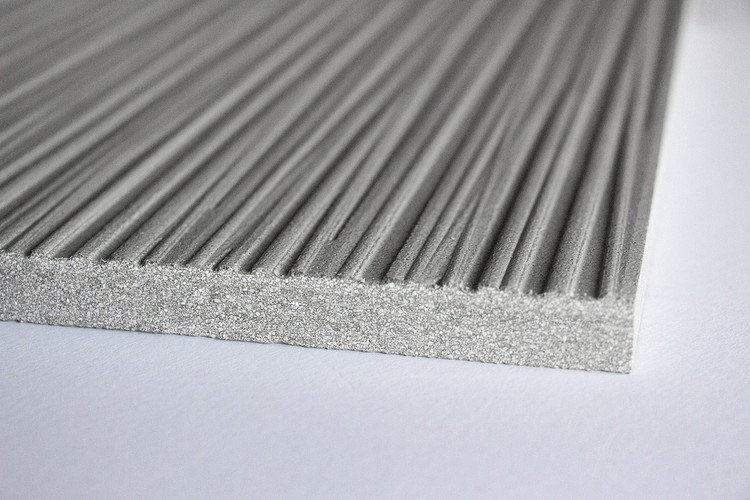
- Automotive Manufacturing
In the automotive industry, lightweighting has become one of the key factors in improving fuel efficiency and reducing emissions. Glass fiber alkali-resistant yarn is widely used in the manufacture of composite materials for automotive body parts, interior parts and other parts due to its light weight and high strength. These materials can not only reduce the total weight of the vehicle, but also enhance the rigidity of the body structure and improve collision safety. - Aerospace
The aerospace industry has extremely stringent requirements for materials, which must ensure both lightness and high strength and temperature resistance. The composite material formed by combining glass fiber alkali-resistant yarn with resin can meet these requirements and is widely used in aircraft fuselages, wing beams, tail wings and other parts. In addition, it also has important applications in rocket shells, satellite antennas and other fields. - Marine Engineering
The marine environment is complex and changeable, and higher requirements are placed on the corrosion resistance and seawater erosion resistance of materials. Glass fiber alkali-resistant yarn is used to make composite components in marine engineering such as hulls and dock facilities due to its good chemical stability, effectively extending the service life of these facilities.
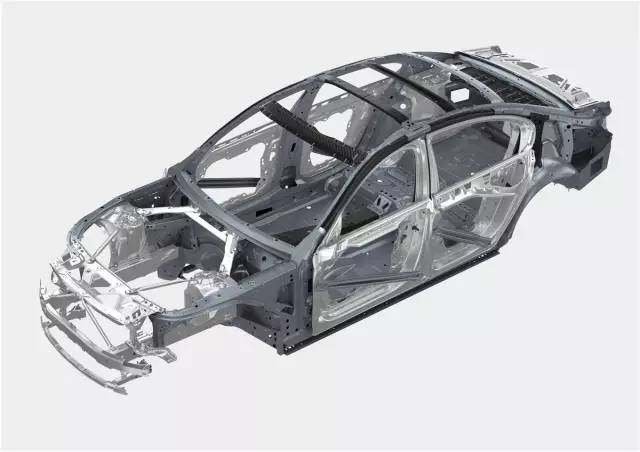
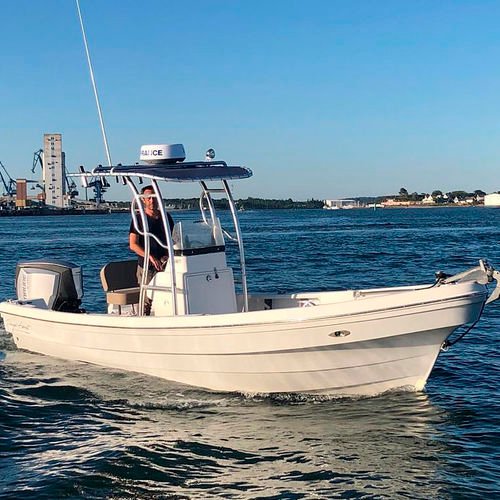
- Circuit Board Substrate
In the electronics industry, glass fiber alkali-resistant yarn is an important component of the substrate of printed circuit boards (PCBs). It provides good insulation performance and can maintain dimensional stability during high-temperature welding, ensuring the reliability and consistency of circuit boards. - Electromagnetic shielding materials
With the increasing functions of electronic products, the problem of electromagnetic interference has become increasingly prominent. Glass fiber alkali-resistant yarn can be used in combination with other conductive materials to make efficient electromagnetic shielding materials, effectively reducing mutual interference between electronic devices and ensuring the clarity and stability of signal transmission.
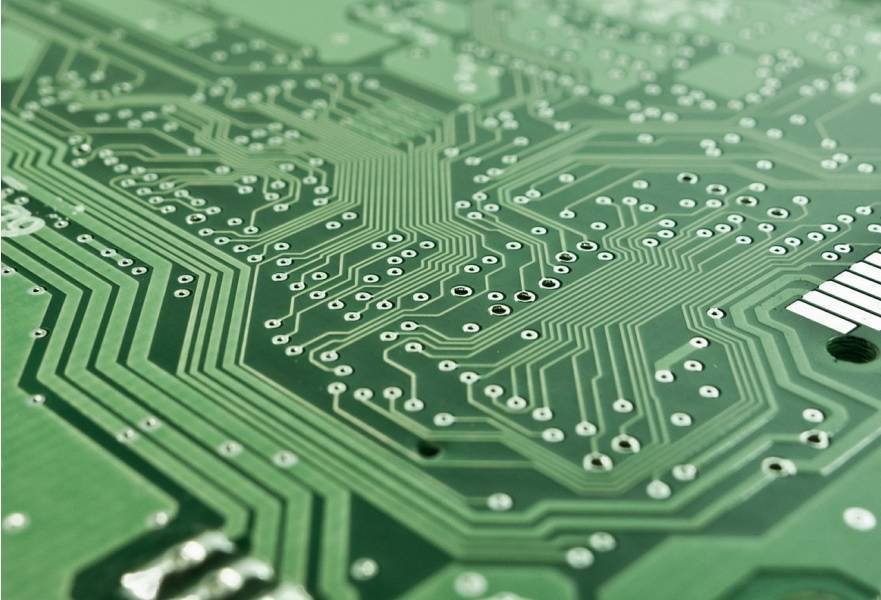
- Chemical corrosion protection
In the chemical industry, glass fiber alkali-resistant yarn is used to manufacture anti-corrosion equipment such as storage tanks and pipelines. These equipment need to withstand the erosion of corrosive media such as strong acids and alkalis. Glass fiber alkali-resistant yarn has become an ideal choice with its excellent corrosion resistance. - Environmental filtration
With the increasing severity of environmental pollution problems, the demand for filter materials is also increasing. Glass fiber alkali-resistant yarn is used to make filter materials in air purifiers and water treatment devices due to its good filtration performance and chemical stability, helping to purify air and water. - Sports equipment
In the manufacture of sporting goods, glass fiber alkali-resistant yarn is also used to make the shaft part of golf clubs, fishing rods and other equipment. These equipment require both lightness and sufficient elasticity, and glass fiber alkali-resistant yarn just meets these needs, making sports equipment more durable and easy to control.
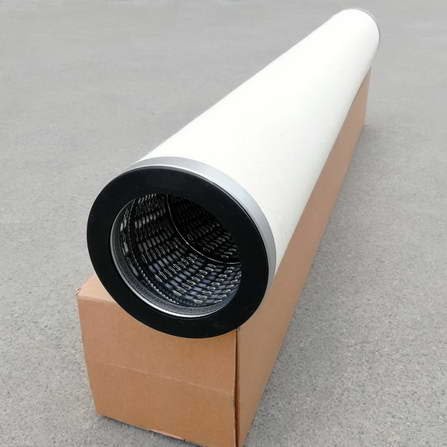
In Conclusion
As a high-performance inorganic non-metallic material, glass fiber alkali-resistant yarn has shown great application value and development potential in many industrial fields due to its excellent mechanical properties, chemical stability and durability. From the initial construction industry to today’s automobile manufacturing, aerospace and even electronics industry, glass fiber alkali-resistant yarn has become one of the indispensable important materials. In this context, Niumaterial, as a fiberglass manufacture focusing on the research and development and production of high-quality glass fiber products, has always adhered to customer demand-oriented, continuous innovation, and is committed to providing users with high-quality and reliable alkali-resistant yarn and other glass fiber products. Whether it is from the selection of raw materials to the optimization of production processes, or from product quality testing to after-sales service support, Niumaterial strives to be excellent. We firmly believe that through continuous technological innovation and service upgrades, Niumaterial can better serve all walks of life and contribute to the development of the glass fiber alkali-resistant yarn industry.